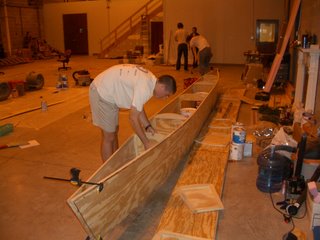
Third day of work and we have one hull framed up and looking sharp. She sure is beautiful and this sight made the whole day of work well worth it. Here is the day's progress report. As of 2am this morning there is no mistaking....its a boat!
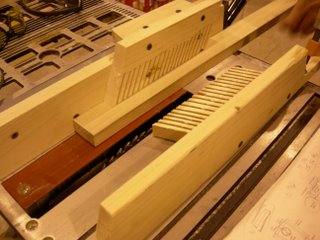
Work began this morning with chines and gunwales that had cured over night. We needed to rip them to the correct dimensions and build a feather board jig for the table saw, in order to do this accurately.
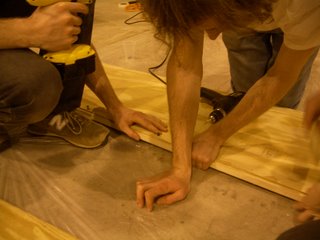
With the chines and gunwales cut to the proper dimensions, we used a spacing jig to set them onto the side panels and screwed them into place. Then we removed the screws to apply epoxy and reassembled to a perfect fit.

Here are all four side panels with gunwales and chines curing. We are also starting to think about the final bulkhead placement and beveling at this point.
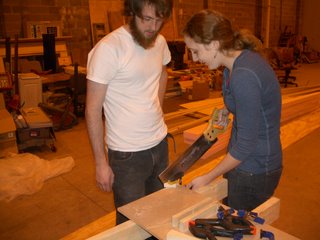
Much thanks to Katherine, Matt and Chris's sister who spent most of the day with us in the shop volunteering to help us work. She proved herself to be very handy with a saw. She also managed to keep us on task, reminding us of what we needed to get done.
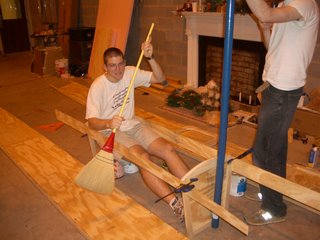
We decided to have one last look at the bulkhead placement and with Mike as the model, we settled on a bulkhead spacing that maximized leg room without much deviation from the plans. The boat is pretty deep; we'll need tallish seats to clear the deck. In this picture, Mike is sitting on a pair of paint cans and a short stack of bricks.
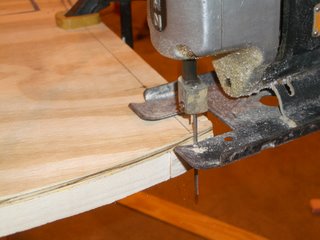
After adding some plywood gussets to the center bulkheads, we planed, sanded, and marked up the bulkheads and started notching them for their final position in the hull.
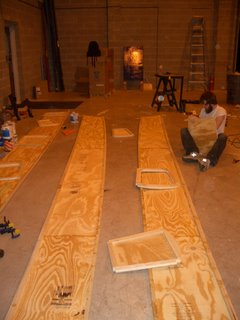
The bulkheads fit without much difficulty and it started getting exciting. Here, Chris is making some fine adjustments to a bulkhead notch for a perfect fit.
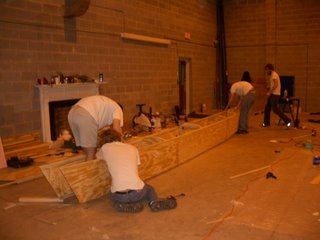
With all the notches finished, the sides went together very quickly. We used temporary wood screws with large washers (to protect the side panel surface) to attach the bulkheads to the side panels for a dry fit of the hull before epoxying.
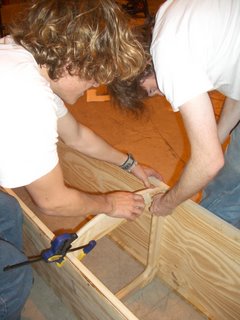
The bulkheads fit right into place. YES!!!
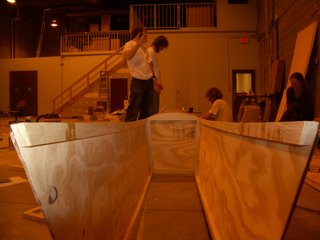
Here are a couple of pictures during the bulkhead/side-panel dry fitting.
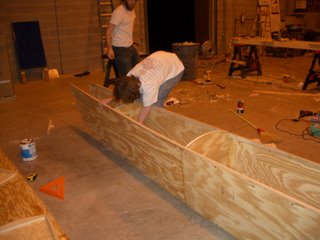
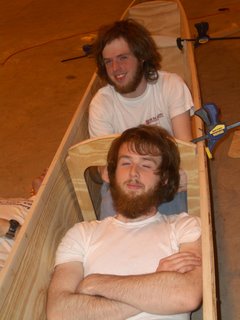
Hmm, how is the fit Matt? We left 54 inches of space between bulkheads for each cockpit. This gives the occupant enough room for to recline into a very comfortable position. I think Chris is asleep. shhhh
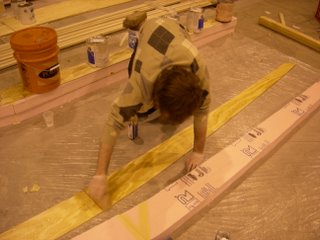
We also finished laminating all of the three inch foam onto the ama frames. We still have to laminate a one inch layer to the outside to get the full width we want. Here, Chris is spreading the polyurethane glue onto the ama before laminating it to the foam.
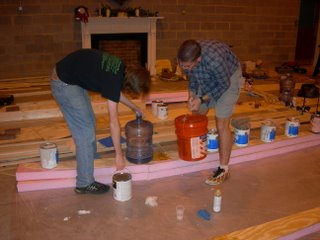
Mike and Matt work on weighing down the ama to cure under compression. Since the polyurethane glue is an expanding type, the pieces have to be well clamped to avoid gappy joints.
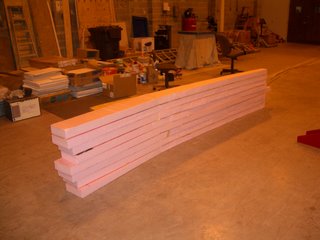
Our stack of finished amas with foam attached. These still need their outer layer, and final shaping into a circular cross-section. The whole team is planning to meet back up after Christmas. Until then, Matt, Chris, and Mike will be working more on the second hull and shaping the amas out of the foam. I will be going back to Chapel Hill for some family time.