
Sunday, December 31, 2006
Saturday Progress

Saturday, December 30, 2006
Nice Bottom!
Next we started squaring up the second hull for assembly following the same procedure as the first boat. By the end of the day we had the second boat all glued up and curing so that tomorrow we could glue the bottom on the second boat and begin applying fiberglass tape to the inside of the first hull.
A Big Square Boat
Once everything was curing on the tops and bottoms, finalizing work started on bulkheads for boat 1. This was one of the most frustrating parts of the build because we had to make sure that the whole boat was more or less in a straight line. We eventually solved the problem by adding diagonal cross braces for each section of the hull. At the end of the day boat 1 was curing with the bulkheads and stem in place.
To see all of our work on the bulkheads check out our time lapse video...cool camera Alan! A picture was taken every 2.5 minutes.
Wednesday, December 27, 2006
Thanks Duckworks!

Outrigger Gluefest
To get the desired 1" of foam we needed on either side of the existing foam-over-plywood outriggers, we ripped the scrap foam on the table saw. This was fast and effective, leaving us with straight 'planks' of foam that we could easily glue in place. The only downside to this kind of cutting is the ultrafine, static-generating pink dust that can easily make a room filling cloud. It sticks in your body hair and eyelashes. We taped cardboard around the legs of our saw and rigged a shop-vac as a dust collector. Otherwise, the dust that coated the table saw controls would have coated the room...
With more polyurethane (off brand Gorilla) glue, we adhered these last sections. Each side of the outriggers got another 4 foam segments. With plenty of masking tape and weight, we laid up one side and went to lunch. After consuming about a pound and a half of tuna, a jar of pickle relish, a small box of alfalfa sprouts, and four fresh sandwich rolls ($9), we flipped them over and glued the other side. Here's one last shot of the drying amas...
With luck we'll begin shaping before the week is out! Thanks for watching us!
Matt Hazard
Saturday, December 23, 2006
Holy Hull: Part Deux
Holy Hull!! (work day 3)
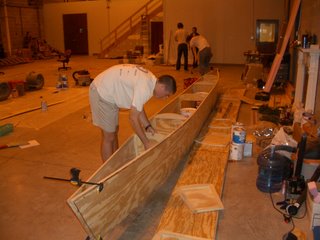
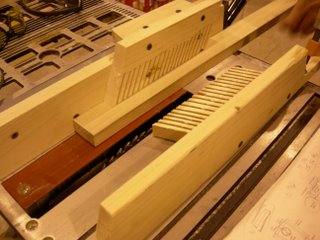
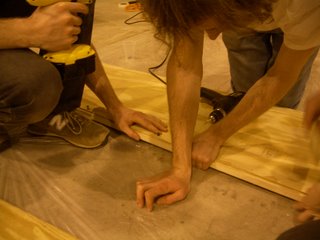

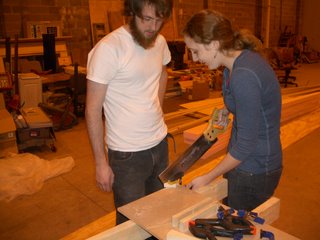
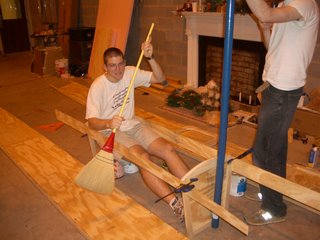
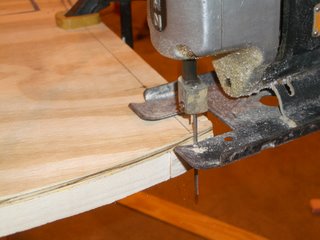
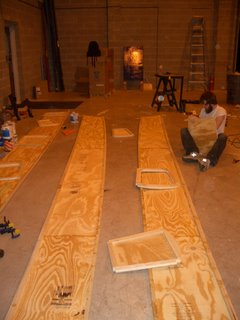
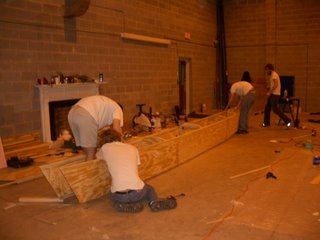
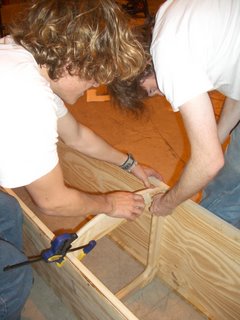
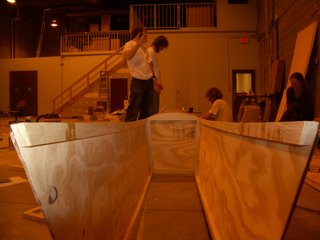
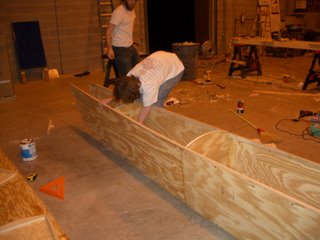
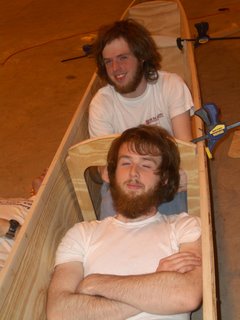
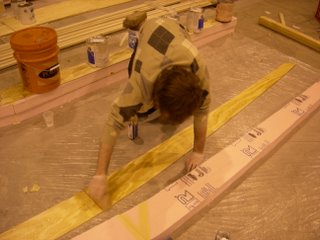
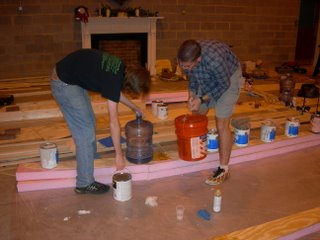
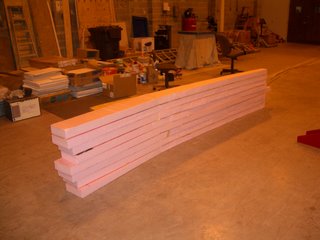
Friday, December 22, 2006
Back to work (work day 2)
Back from a long day of work at the warehouse today (Thursday). We got to work laying up the rest of the side panels so they could cure during the day and then Chris and Mike went in search of some foam to use for the ama construction. Meanwhile, Matt and I started work on the gunwales and chines scarfing and gluing long hardwood boards together that will make up the stringers.
Here are the gunwales and chines curing under compression. The joints overlap at a shallow angle similar to the scarf joints used in the side panels to maximize the glued surface area and balance the normal and shear loads in the joint.
Trimming the excess fiberglass from the edges of the ama panels. These joints are strong!
With Mike and Chris back with the foam, we started working on cutting strips to laminate to the plywood panels to make up the structure of the amas that will later be shaped to the final ama shape and then fiberglassed. We used expanding polyurethane glue to laminate the foam to the plywood, it for the application.
While the amas were drying we got to work assembling the bulkhead structure. Each plywood bulkhead has a hardwood perimeter around it that aids in attaching the sides, bottom and deck. Here is the number 2 bulkhead with the hardwood glued in place. The end of day two we managed to finish all of the bulkheads, all of the chines and gunwales and all of the side panels. A very long day but very rewarding.
Some real progress
The team and vehicles are relocated for now in Charlotte, NC and we have set up camp in the warehouse attached to Hubert Whitlock Builders, a local contractor owned by Chris and Matt's family. The large heated space is ideal and much progress has been made. Here we are on Wednesday after unloading the trailer exited to get some real work done. Read on!
The view from above in the new workspace showing our side panels laid out for labeling as we prepare to make that scarf joints and join the side panel pieces together. It was a big help to be able to spread everything out on the floor and organize all of our parts.
The finished scarf joints ready for joining. The scarf joint making jig worked flawlessly after the 5th or 6th try on some scrap plywood getting everything lined up juuuuust right. The joint was made with thickend epoxy and compressed with weights.
At the end of day one we have half of the scarf joints laid up and curing and our four ama sections laid up on the far left one on top of the other. The ama pieces were joined with butt joints and sandwiched between a layer of 4 inch wide strip of 8oz fiberglass cut on the bias top and bottom. We were a little short on heavy things so everything in the room turned into a weight to help compress the joints. All in all, a good first day.
Sunday, December 17, 2006
Back to Work
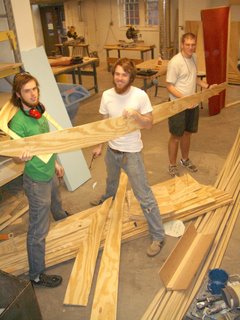
Above are the front ama sections that will be joined with the rear sections and laminated in between thick blue foam and shaped to the final ama profile.
This jig was made to cut the scarf joints into the hull side panels that require a very low angle cut for making the joint.
Here is the shop bot in action cutting out the ama panels. We were able to cut all of the panels for all 4 amas out of one sheet of plywood!
Wednesday, December 13, 2006
Fiberglass

Now the only major things left to buy are Epoxy, masts, blue foam, and all of our required equipment; we hope to get things taken care of before we break for the semester. Speaking of the break, the current plan is to move everything to Charlotte and go on a 2-3 week building blitz so the majority of the canoes are done before school starts up again. Look for more updates in the coming weeks, we hope to have great progress.
Wednesday, November 15, 2006
Big Canoes
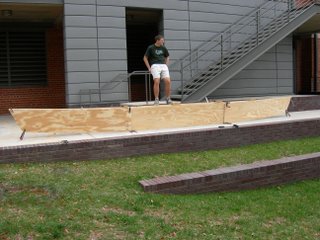

They look ready to take on the Manatees.
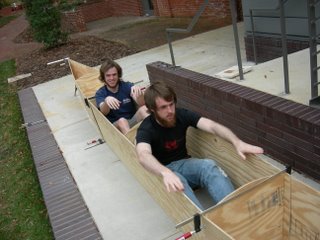
One of the design school shop workers knows a thing or two about homebuilt boats, and he asked us how long the race was, we responded "300 Miles" and he said that the sea wasn't that deep. The next picture puts his words into a visual form.
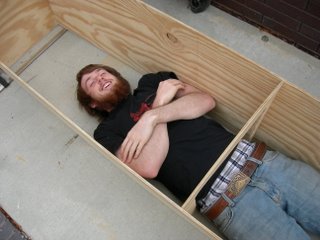
Sunday, November 12, 2006
Tiny Canoes

Cutting out the bulkheads and side panels on the laser cutter and assembling the boats in miniature was a really good exercise for the overall construction of the boats. With some more work tomorrow, we hope to have the ShopBot up and running and get some full sized boat pieces cut out. Below are some more picture of the models.
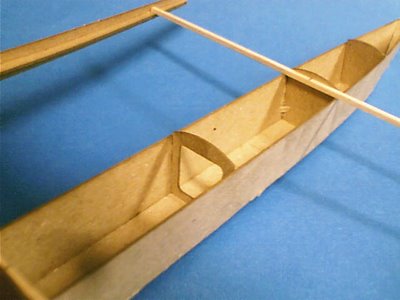
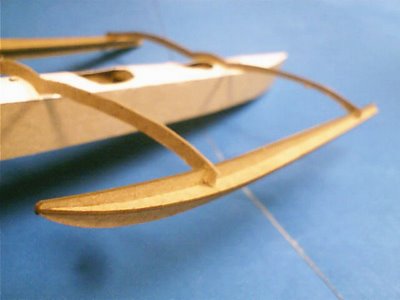
Thursday, November 09, 2006
We've Got Wood! ... for building boats
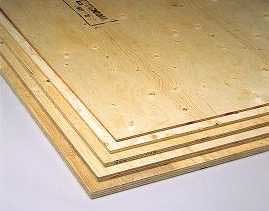
We will use a shop-bot that we have access to at school to cut out our bulkheads and side panels. That should make quick and accurate work of the “curvy pieces” so that we can begin assembly. The shop-bot shown here is basically a 3-axis router that can cut 4x8 sheets of wood to exact shapes based on a CAD file. Here is a picture of one.
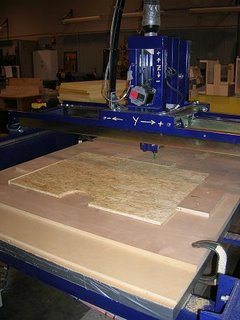
We plan to modify the deck to more fully enclose the canoe and allow for cockpits to be cut so that we can outfit the boat with spray-skirts. We will also be designing our mast step and outrigger crossbeam mounting cradles into the hull as well as all the necessary storage compartments, hatches and closed cell foam buoyancy compartments.
We hope to begin cutting, shaping, and assembling this weekend so stay tuned for pictures and information.
Tuesday, October 17, 2006
Canoe building plans

There are many other interesting and easy to build sailing canoes on the outrigger Sailing Canoes website so please take a look.
The Wa'apa is a three board canoe that is very simple to built. A three board canoe is so named because that is how it is built. There are a couple of designs for this boat including a shunting version and a tacking version. It is also possible to build the boat such that it can be broken into 8 foot sections that bolt together at bulkheads.
We would plan to build two identical boats that would have the capability to be sailed or paddled individually or connected and sailed together in a catamaran configuration for use in our 4 man team entry in the Everglades Challenge in 2007.
Canoe Sailing on Jordan Lake
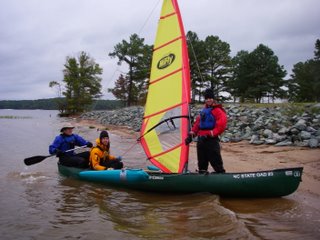
To the lake we went. We were able to all pile in which was a good test of a boat loaded with gear even if this wasnt the boat we would use.
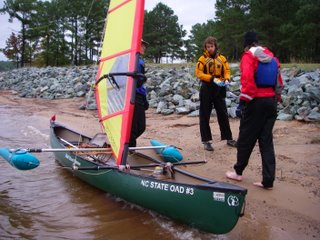
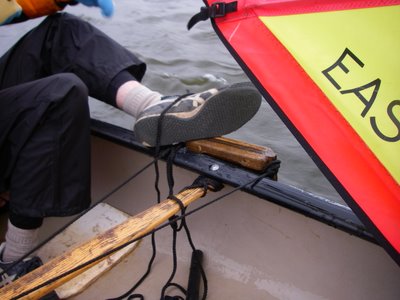